La medida del Overall Equipment Effectiveness (OEE) o Eficiencia General de los Equipos, y en algunas partes del mundo, también conocido como TVC (Tiempo, Velocidad y Calidad) es una forma de medir el impacto total que causan la calidad, productividad y disponibilidad en el desempeño de una máquina.
Se calcula multiplicando los porcentajes de desempeño del equipo en cada una de estas áreas:

Ejemplo:
Si se conoce que una maquina prensadora puede operar a 100 golpes por minuto y actualmente opera a 80 golpes por minuto, además que durante el mes tiene una disponibilidad del 85% del tiempo y un nivel de piezas de mala calidad del 10%, aplicando la formula tenemos:
80% x 85% x 90% = 61%
Valor de OEE |
Calificación |
Observación |
OEE < 65% |
Inaceptable |
Se producen importantes pérdidas económicas. Muy baja competitividad. |
65% < OEE < 75% |
Regular |
Aceptable sólo si se está en proceso de mejora. Pérdidas económicas. Baja competitividad. |
75% < OEE < 85% |
Aceptable |
Continuar la mejora para superar el 85 % y avanzar hacia la World Class. Ligeras pérdidas económicas. Competitividad ligeramente baja. |
85% < OEE < 95% |
Buena |
Entra en Valores World Class. Buena competitividad |
OEE > 95% |
Excelencia |
Valores World Class. Excelente competitividad |
La OEE considera 6 grandes pérdidas:
Pérdidas |
Afectan a |
Paradas/Averías |
Disponibilidad |
Configuración y ajustes |
Pequeñas paradas |
Rendimiento |
Reducción de velocidad |
Rechazos por puesta en marcha |
Calidad |
Rechazos de producción |
Disponibilidad: es el resultado de dividir el tiempo de operación (TO) entre el tiempo planificado de operación (TPO).
TPO= Tiempo Total de trabajo - Tiempo de Paradas Planificadas
TO= TPO - Paradas y/o Averías
Disponibilidad = (TO / TPO) x 100 (se expresa en porcentaje)
Productividad: es el resultado de dividir la cantidad de piezas realmente producidas por la cantidad de piezas que se podrían haber producido. La cantidad de piezas que se podrían haber producido se obtiene multiplicando el tiempo en producción por la capacidad de producción nominal de la máquina.
La capacidad de la máquina/línea declarada en la especificación se mide en número de unidades / hora.
Productividad = Nº Total unidades / (tiempo de operación x velocidad máxima)
La productividad se expresa en porcentaje.
Calidad: esta característica tiene en cuenta toda la fabricación de productos rechazados por la maquina o calidad del producto. Se mide en tanto por ciento de unidades no conformes con respecto al número total de unidades fabricadas.
Nº de unidades conformes calidad = Nº de unidades totales producidas - Nº de unidades no conformes
Calidad = Nº de unidades conformes/Nº unidades totales
La calidad se expresa en porcentaje.
El TPM (Total Productive Maintenance o Mantenimiento Productivo Total) se centra en la eliminación de pérdidas ocasionadas o relacionados con los paros, calidad y costos en los procesos de producción.
En contra del enfoque tradicional del mantenimiento, en el que unas personas se encargan de producir y otras de reparar cuando hay averías, el TPM aboga por la implicación continua de toda la plantilla en el cuidado, limpieza y mantenimiento preventivo, logrando de esta forma que no se lleguen a producir averías, accidentes o defectos.
Para comprender mejor el significado del TPM hay que entender que éste se sustenta en 8 pilares:
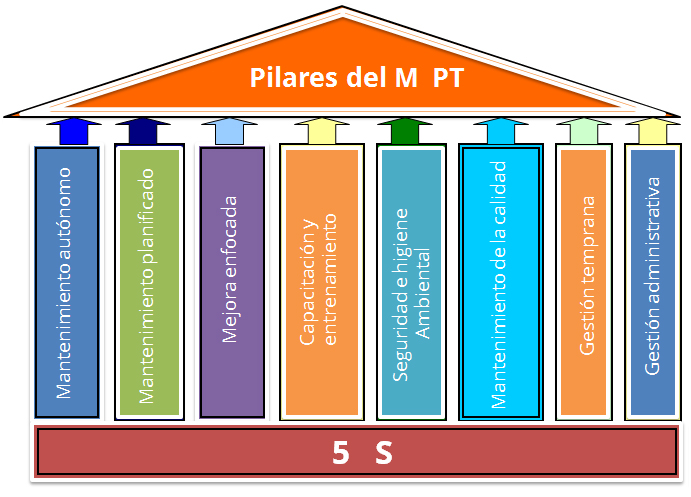
Haz clic para revisar la información
En este pilar se maximiza la eficiencia global de los equipos y de los recursos humanos en los procesos de producción dentro de la planta, todo esto se realiza mediante un trabajo organizado en equipos, empleando técnicas específicas y centrando la atención en la eliminación de los desperdicios que se presentan en las plantas industriales.
Es básicamente la prevención del deterioro en los equipos y componentes, consta de un conjunto de actividades que son realizadas diariamente por todos los trabajadores en los equipos que operan. Los operarios deben ser capacitados de manera que tengan los conocimientos necesarios para operar los equipos correctamente.
El propósito de este pilar consiste en la necesidad de avanzar gradualmente en la búsqueda de la meta: cero averías para una planta industrial. El mantenimiento planificado sugerido por el Instituto Japonés de Mantenimiento de Plantas (JIPM) se implanta en 6 pasos.
- Identificar el punto de partida del estado de los equipos.
- Eliminar el deterioro de los equipos y mejorarlo.
- Mejorar el sistema de gestión para la información.
- Mejorar el sistema de mantenimiento periódico.
- Desarrollar un sistema de mantenimiento periódico.
- Desarrollo superior del sistema de mantenimiento periódico.
Es una clase de mantenimiento preventivo orientado al cuidado de las condiciones del producto resultante, es así que este pilar tiene como objetivo, facilitar la operación de los equipos donde se generen defectos de calidad mediante la prevención, lo que certifica que la maquina cumpla las condiciones para lograr cero defectos en el producto.
Este pilar es exclusivo ya que es aplicable en las empresas innovadoras donde la actualización de equipos es continua. Esta restricción es debido a que las actividades de mejora de este pilar, se dan en la fase de diseño y construcción inclusive en la puesta a punto de los equipos, focalizándose en la reducción de costos durante la producción.
Para evaluar este pilar se inicia con medición de las pérdidas del sistema productivo, consecuentemente el autodesarrollo y la práctica son factores importantes para lograr una transformación de la cultura de trabajo existente en la empresa, con lo cual se adquiere un compromiso y resultados efectivos tanto en la productividad como en el comportamiento humano.
Los principios fundamentales de este pilar son:
- Eliminar pérdidas producidas por la falta de habilidades del personal operativo y mantenimiento.
- Eliminar las pérdidas del sistema de liderazgo y educación utilizado en la empresa para el desarrollo de capacidades.
Todas las actividades asociadas a proyectos de ingeniería e intervenciones de montaje y mantenimiento, están permanentemente expuestas a grandes y pequeños riesgos de accidentes, lamentablemente la mayoría de los accidentes se debe a una gestión deficiente en relación a la prevención.
Este pilar está dirigido directamente a las áreas administrativas, ya que éstas influyen directamente en el costo del producto en las etapas de diseño y desarrollo del sistema de producción, evitando así perdidas de información, coordinación en las actividades respectivas, orden y entrega de materia prima, entre otros factores importantes. Para lograr estos objetivos se utilizan técnicas o estrategias utilizadas en el mantenimiento autónomo.
El mantenimiento autónomo es una de las etapas de la preparación de las condiciones de implantación del TPM y es la acción más difícil y que más tiempo lleva en realizar, por lo difícil de dejar la forma habitual de trabajo.
Los operarios se pueden entrenar y autorizar para realizar cualquier tarea de mantenimiento rutinaria:
- Ellos pueden alertar al grupo de mantenimiento
- Ellos pueden proveer información excelente
- Ellos pueden realizar tareas de mantenimiento rutinarias que se determinen como seguras y apropiadas por el equipo de TPM
Hasta el 75 % de los paros pueden detectarse y prevenirse con un operario bien entrenado.
El mantenimiento autónomo consta de 7 pasos para su implementación:
Paso 1: Limpieza e inspección
En esta primera etapa se busca alcanzar las condiciones básicas de los equipos y establecer un sistema que mantenga esas condiciones básicas durante las etapas uno a tres.
Una limpieza profunda exige que el operario tenga contacto con cada una de las partes y componentes del equipo. Esta actividad produce un mayor interés para evitar que el equipo se ensucie nuevamente. En esta primera etapa, es posible que el operario no logre comprender inicialmente la importancia de la limpieza o que esta debe realizarla personal diferente a ellos. Algunos operarios dedican un poco de tiempo para lavar, soplar aire al equipo, no comprendiendo que este tipo de situaciones pueden producir problemas serios al equipo.
Paso 2: Establecer medidas preventivas contra las causas de deterioro forzado y mejorar el acceso al área de difícil.
En esta etapa se pretende que el trabajador descubra las fuentes profundas de la suciedad que deteriora al equipo y tome acciones correctivas para prevenir su presencia. Se busca mejorar el acceso a sitios difíciles para la limpieza, eliminación de zonas donde se deposita con facilidad la suciedad y se mejora la observación de los instrumentos de control. Esta etapa es importante para el desarrollo de las actividades Kaizen o de mejora continua y son desarrolladas por los propios trabajadores que enfrentan las dificultades en la limpieza o el manejo de los procesos asignados. Los resultados se manifiestan en la mejora del sitio de trabajo, reducción de posibles riesgos y reducción del deterioro acelerado de los equipos debido a la contaminación
Paso 3: Preparación de estándares para la limpieza e inspección
Con base en la experiencia adquirida en las etapas anteriores, se preparan los estándares de inspección con el propósito de mantener y establecer las condiciones óptimas del estado del equipo. Es frecuente emplear las dos últimas S de la estrategia de las 5S con el objeto de garantizar disciplina y respeto de los estándares.
Esta etapa es un refuerzo de aseguramiento de las actividades emprendidas en las etapas 1 y 2. Se busca crear el hábito para el cuidado de los equipos mediante la elaboración y utilización de estándares de limpieza, lubricación y apriete de tornillos, pernos y otros elementos de ajuste, así como prevenir deterioro del equipo manteniendo las condiciones básicas de acuerdo a los estándares diseñados.
Estos estándares en lo posible deben ser preparados por el operador una vez se haya capacitado para realizar esta labor. Como consecuencias, el trabajador participará efectivamente en todas las actividades de cuidar el equipo, iniciando su intervención desde el mismo momento en que prepara las normas de cuidado de los equipos
Paso 4: Inspección general orientada
En los pasos 1,2 y 3 se han implantado actividades orientadas a la prevención del deterioro a través de la mejora de las condiciones básicas de la planta. En el paso 4 y 5 se pretende identificar tempranamente el deterioro que puede sufrir el equipo con la participación activa del operador.
Estos pasos requieren de conocimiento profundo sobre la composición del equipo, elementos, partes, sistemas, como también sobre el proceso para intervenir el equipo y reconstruir el deterioro identificado. Las inspecciones iniciales las realiza el operador siguiendo las instrucciones de un tutor especialista.
Para la implementación del paso cuatro se deben tener en cuenta los siguientes puntos.
- Preparar el programa de formación para operarios, dirigido a lograr un alto conocimiento sobre métodos de inspección.
- Desarrollar el programa de formación empleando la metodología aprender haciendo.
- Desarrollo de las primeras inspecciones con tutor. En esta oportunidad los expertos de mantenimiento podrán apoyar esta clase de tareas.
- Realizar reparaciones e intervenciones livianas con la ayuda del tutor.
- Planificar las acciones de reparación y de nuevas revisiones o inspecciones del equipo. Es necesario contar con plan de inspecciones rutinario. El ciclo Deming será de gran ayuda para impulsar esta clase de acciones en forma rutinaria.
Paso 5: Inspección autónoma
Se evalúan los estándares de limpieza, lubricación y apriete, establecidas en las etapas previas, se mejoran sus métodos y tiempos en base a la experiencia acumulada por el operador.
Las principales actividades de esta etapa están relacionadas con el control de los equipos y la calidad de los mismos, condiciones y estado de ellos como de las herramientas. Una de las aportaciones más significativas del paso cinco consiste en el incremento de la eficiencia de la inspección, al mejorar métodos de trabajo y los estándares utilizados.
El desarrollo del paso cinco incluye los siguientes trabajos prácticos:
- Evaluar los procedimientos utilizados hasta el momento en las actividades autónomas, por ejemplo los estándares de limpieza, lubricación y apriete. Las preguntas más frecuentes son: ¿los tiempos que utilizamos son los mejores?, ¿hemos dejado pasar fallas?, ¿existe recurrencia de fallas?, ¿se han presentado errores de inspección?, ¿el manual de inspección que utilizamos realmente está completo?, ¿podremos incorporar otro punto al manual de inspección?
- Se analizan los estándares para identificar si se pueden eliminar algunos puntos de inspección de alta fiabilidad, realizar trabajos en paralelo para reducir los tiempos de inspección, ¿podremos transferir algunas de estas actividades de inspección al trabajo de limpieza?
- Se evalúan los controles visuales que hemos utilizado. ¿Son adecuados?, ¿han ayudado a mejorar la inspección?, ¿faltan puntos?, ¿se pueden introducir nuevos elementos transparentes para facilitar la inspección visual?, ¿los códigos de colores que hemos utilizado para facilitar las operaciones realmente han aportado mejoras, o se deben realizar modificaciones para detectar con facilidad los problemas?
Paso 6: Estandarización
Una vez se han logrado las mejoras de los métodos de inspección para los equipos propuestos en el paso cinco, es necesario establecer un estándar para que éstos se mantengan a través del tiempo. Se busca que estas actividades de rutina sean asignadas adecuadamente a los operarios y en el mejor tiempo.
Los estándares deben incluir los sistemas de información necesarios para garantizar que los resultados de la inspección autónoma se emplean para la mejora del equipo y la prevención de problemas potenciales.
Se pueden resumir los siguientes puntos como los objetivos esperados en esta etapa de mantenimiento autónomo:
- Analizar las funciones de los operarios desde el punto de vista de las tareas asignadas, estándares de trabajo, eficiencia con la que se desarrollan, tiempos utilizados y coherencia.
- Desarrollo de acciones Kaizen para mejorar las acciones de trabajo e inspección y control de los equipos.
- Asegurar la unidad de criterio entre los diferentes operarios que actúan sobre un mismo equipo en diferentes turnos.
Paso 7: Control autónomo total
En los pasos 1 a 6 se logran resultados de mejora tanto en el control de los equipos como en el cumplimiento de estándares mejorados de los métodos de trabajo. En el paso 7 se integra plenamente el proceso de mantenimiento autónomo al proceso de dirección general de la compañía o dirección por políticas.
Se pretende reconocer a la capacidad de autogestión del puesto de trabajo del operador, creando un sentimiento de participación efectiva en el logro de las metas y objetivos de la fábrica y de la empresa.
El operario podrá tomar decisiones en el ámbito de su puesto de trabajo, cooperará para el logro de objetivos compartidos, realizará nuevas acciones Kaizen y se inician en nuevas fronteras de mejora e innovación permanente en la forma de trabajar. Es en esta etapa donde realmente se logra que una planta de producción sea en las palabras de un directivo de Chaparral Steel un verdadero laboratorio de aprendizaje.
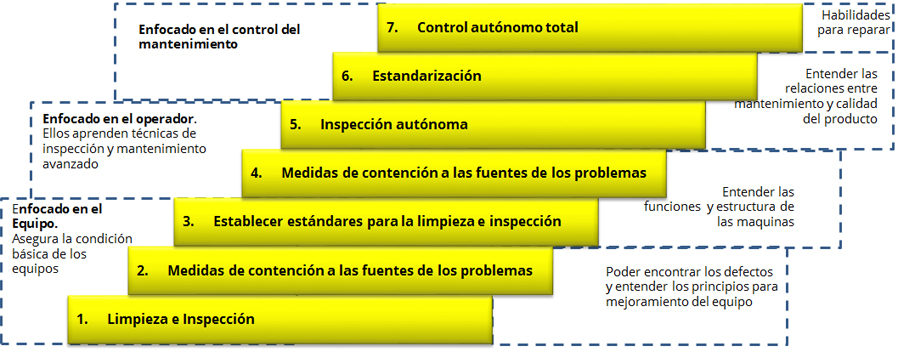
Para la implantación del mantenimiento autónomo se debe seleccionar el área donde se va a realizar la primera aplicación. De acuerdo a nuestra experiencia, es más viable aquella área donde ya se hayan desarrollado actividades de mejora enfocada o Kaizen, debido a que el personal está más sensibilizado sobre los problemas que producen la falta de aseo y limpieza. Sin embargo, no se debe descartar la posibilidad de iniciar las actividades en otras áreas, especialmente aquellas donde la falta de limpieza es apreciable y cualquier mejora brinde satisfacciones y ejemplo para otras.
Una buena práctica consiste en iniciar el mantenimiento autónomo con dos experiencias debido a la posibilidad de comparar sus avances. No intente tomar una planta completa para realizar la primera etapa del mantenimiento autónomo. Es muy difícil poner en marcha un proyecto de tal magnitud sin una preparación previa. Es mejor iniciar una experiencia reducida debido a que se pueda controlar mejor su avance y probar metodologías, procedimientos, auditorías, formatos y la forma de entrenar al personal. Con esta experiencia acumulada se procede a escribir en un manual de la experiencia piloto. Se debe registrar todo lo sucedido y el conocimiento adquirido durante la realización de la experiencia en la etapa 1. Este manual servirá para iniciar experiencias similares en otras áreas de la planta. De esta forma se va progresando en cada una de las etapas, pero siempre se tiene una experiencia de referencia más avanzada.