El Mapa de Cadena de Valor o Value Stream Map es una herramienta que sirve para ver y entender el proceso e identificar sus desperdicios, permitiendo detectar fuentes de ventaja competitiva. Ayuda a establecer un lenguaje común entre los todos usuarios y comunica ideas de mejora enfocadas en la utilización de un plan, priorizando los esfuerzos de mejoramiento.
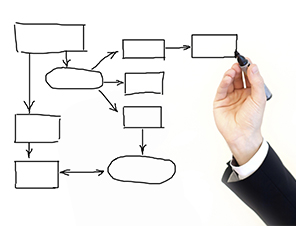
Un mapa de cadena de valor muestra la secuencia o movimiento de lo que el cliente valora. Incluye materiales, información y procesos que contribuyen a obtener lo que el cliente le interesa y compra.
Consiste en la técnica de dibujar un mapa o diagrama de flujo, mostrando como los materiales e información fluyen “puerta a puerta” desde el proveedor hasta el cliente, y busca reducir y eliminar desperdicios, pudiendo ser útil para la planeación estratégica y la gestión del cambio.
A Toyota se le atribuye el origen del uso del VSM con el nombre de Mapa del Flujo del Material e Información. Aunque esta herramienta se originó para usarse en procesos de manufactura, es ampliamente usado en procesos administrativos.
Existen diferentes tipos de formatos de diagramas de flujo (Spagueti, Tortuga, SIPOC); SIPOC (Supplier-Inputs-Process-Outputs-Costumer) es el más utilizado por su sencillez y facilidad didáctica, se puede usar como la base de partida de la elaboración del VSM.
Tipos de actividades en un mapa de cadena de valor
Las actividades que dan valor añadido o agregado son aquellas por las que el cliente está dispuesto a pagar, son las que está esperando para satisfacer su requerimiento y resolver su necesidad. Existen otras actividades dentro de la empresa productora o de servicios que se requieren para su operación, pero que no agregan valor desde el punto de vista de las ventajas para el cliente; estas actividades se tienen que reducir al máximo sin afectar las políticas internas de la empresa.
Además existen actividades que no agregan valor ni al cliente ni a la empresa y son un verdadero desperdicio de recursos, éstas se deben de eliminar.
Tipos de desperdicios en el pensamiento esbelto (lean)
Todos los sistemas son perfectibles y el objetivo que buscan las empresas es lograr un proceso o servicio que dé sólo lo necesario con la calidad que el cliente espera en el menor tiempo posible. Lo que mueve a las empresas esbeltas es dar sólo lo que el cliente está dispuesto a pagar.
Los siete desperdicios más comunes aceptados en el sistema de producción son los siguientes:
- Sobreproducción
- Tiempo de espera
- Transporte
- Proceso inadecuado
- Inventarios innecesarios
- Defectos
- Movimiento
Sin embargo, el mayor de los desperdicios que puede existir y no se enumeró es el desperdicio del talento, ya que el recurso más valioso que puede tener cualquier empresa es el equipo humano que logre integrar.
12.2 Elaboración de un VSM
A continuación se presenta una guía para realizar un VSM:
Etapa 1: Identificar la familia del producto
- Se debe seleccionar un grupo de 3 a 5 personas que conozcan el proceso que se va a mapear. Deben recorrer el proceso o sistema buscando captar todos los detalles. Éstas deben ser personas con actitud positiva al cambio y mente abierta. Seleccionar de entre ellos al líder que coordina las actividades y que tenga la capacidad de mantener al equipo enfocado en lograr resultados.
- Después de que el equipo seleccionado conoce el procedimiento a seguir, deberá caminar varias veces a lo largo de toda la cadena de valor que será mapeada de principio a fin, es decir, de puerta de entrada de materia prima de los proveedores a puerta de salida de los productos al cliente. Si se ven todos los detalles del proceso, se debe usar las 5W (why, who, when, whay, where) para comprender con detalle por qué se hacen las cosas como se hacen actualmente.
- Seleccionar uno de los criterios que se pueden utilizar para agrupar productos cuando existe una gama de productos muy grande de los mismos.
- Se debe limitar el mapa sólo a una familia de productos, elegir la familia de productos que tengan un mayor impacto en los requisitos del negocio.
Etapa 2: Diagrama del estado actual
Un mapa del estado actual muestra los procesos/sistemas de trabajo como actualmente existen.
Esto es vital para entender las necesidades para el cambio y para entender dónde se encuentran las oportunidades de mejora. El grupo seleccionado deberá confiar exclusivamente en sus observaciones, tiempos cronometrados por ellos, e información que los miembros del grupo obtengan; deben apegarse a sus anotaciones de lo que se hace actualmente y no a lo que debería de estarse haciendo con base en su criterio. Lo que se desea es corregir en un futuro próximo malos hábitos y procedimientos mal entendidos y usados porque “siempre se ha hecho así”.
Etapa 3: Mapeo del estado futuro
El mapeo obtenido del estado futuro del mapa de cadena de valor ayuda a desarrollar la estrategia de manufactura esbelta.
Es conveniente contar con conocimientos de las demás herramientas de pensamiento esbelto (lean). Para diseñar un estado futuro, ayuda a conocer: Kanban, Células de Manufactura, SMED, Poka Yoke, etc. Aunque no es indispensable y pudiese crear confusión, como sucede cuando se mapea un proceso administrativo.
Lo único que se busca es establecer lo que se necesita que ocurra y cuándo debe ocurrir para mejorar el proceso actual.
Para construir el mapa del estado futuro se usa el mapa del estado actual, y es necesario:
Crear una gráfica de ciclo tiempo Takt: con los datos recolectados y calculados durante la elaboración del estado actual del VSM se puede trazar la gráfica del ciclo de tiempo takt; esta gráfica compara los ciclos de tiempo individual dentro del ciclo de tiempo takt del proceso/sistema. Lo cual ayuda a determinar cómo y qué se debe mejorar en el futuro.
Identificar el proceso cuello de botella: es la operación con el tiempo de ciclo de valor agregado que exceda el takt time, por ejemplo: si se tiene un proceso que consume 44 segundos, y si el cliente incrementa su demanda bajo las mismas condiciones se podrá convertir en un cuello de botella, y además se reduce el tiempo disponible real por efecto de incrementarse el tiempo de paro del equipo, ya sea por falta de mantenimiento adecuado, mayor número de inversiones, etc. El escenario de una restricción se vuelve más factible, es importante monitorear este tipo de acciones para prever acciones y tener un plan de contingencia, ya que un embudo:
- Determina la producción del sistema total.
- Llega a ser un punto primario del programa.
-
Calcular el tamaño óptimo de los operadores e identificar las estaciones de trabajo potenciales: la gráfica takt time demuestra que los procesos están desbalanceados en los tiempos que consume, debiéndose balancear el trabajo determinando el tamaño óptimo de los operadores necesarios y buscando hacer un flujo continuo.
Para hacer esto se necesita tomar el tiempo total del ciclo y dividirlo entre el tiempo takt, redondeando el valor obtenido y la unidad superior completa, normalmente aumentando ligeramente la cantidad de operadores.
Sin embargo, si a pesar de ello no se logró la reducción de tiempo total del ciclo que sea igual o menor del tiempo takt, la cantidad de operadores se debe volver a reducir, quedando como estaba originalmente la cantidad de operadores y estableciendo una célula de manufactura que puede ser arreglo “U” o de otra forma según convenga al proceso.
-
Decidir si se crea un aprovisionamiento de supermercado o se envía al cliente por pedido: se debe decidir qué tipo de modelo de distribución se desarrollará. ¿Se crea un supermercado de productos terminados o se embarcarán los productos terminados directamente al cliente?
Si la empresa sólo produce un producto y la demanda es relativamente estable, lo más lógico es crear un modelo de distribución por órdenes específicas.
Debido a que la gran mayoría de las compañías producen más de un producto y existen inexactitudes en los pronósticos de ventas de casi todas las empresas, lo que tiene mayor lógica es crear un supermercado reducido (inventario muy reducido).
Esto parecía ilógico ya que va en contra de la producción en masa y las economías de escalas, por no producir todo lo que es posible y que esté limitado sólo por la capacidad de la planta, sin embargo, la gran diferencia es que aquí nosotros controlamos el nivel del inventario en lugar de que el nivel de inventarios nos controle como en un sistema push (empujar el producto).
-
Nivelación de la mezcla de la producción en un proceso marcapaso: se debe distribuir equitativamente la producción de los diferentes productos en el proceso marcapaso.
Agrupar los productos hace difícil servir a aquellos clientes que necesitan algo diferente que entregas por lotes producidos en dicho tiempo. Las entregas en tiempo se afectan.
Determinar la localización Kanban: cuando se crea un supermercado se debe tener una forma de señalización de cuándo producir y cuándo no hacerlo; se puede hacer en diferentes formas, en este documento se opta por el sistema Kanban, establece la orden inmediato de qué y cuánto se debe producir.
Mejorar las comunicaciones y programación: ahora corresponde mejorar las comunicaciones en lugar de programar cada proceso de forma individual, se lleva a cabo de una forma global como un todo.
El propósito del mapeo de la cadena de valor es hacer resaltar la causa del desperdicio y eliminarlos o al menos reducirlos para la implementación de un estado futuro de la cadena de valor que puede convertirse en realidad en un periodo de tiempo corto en adición de crear un vínculo para mejorar la comunicación y confianza entre todos los involucrados, creándose una atmosfera e colaboración y unidad de grupo que se extenderá y repercutirá positivamente con el cliente.
El objetivo es construir un cambio de producción donde el proceso individual es conectado hacia sus clientes, ambos para flujos continuos, y cada proceso consigue cerrar de la mejor manera posible para producir sólo lo que el cliente necesita y cuando lo necesita.
- Cuestionamiento de que debe uno hacer para complementar el estado futuro: asumiendo que usted está trabajando para una empresa existente, con un producto y proceso existente, algunos de los desperdicios en el flujo de valor serán el resultado del producto diseñado, el proceso de maquinaria ya adquirida y el sitio remoto de algunas actividades.
Estas fases del estado actual probablemente no puedan ser cambiadas inmediatamente. A menos que esté envuelto en una nueva introducción de un nuevo producto, la primera interacción de su mapa del estado futuro debe tener diseños de productos, procesos tecnológicos y sitios de planta que dieron y tratan de remover tan rápidamente como sea posible todas las causas de desperdicio no causado por estas fases.
Preguntas clave para elaborar un estado futuro
- ¿Cuál es el tiempo takt, basado en el tiempo de trabajo disponible de los procesos más cercanos al cliente?
- ¿Llevará a cabo un supermercado de productos terminados desde el cual el cliente los jalará o serán embarcados directamente al cliente?
- ¿Dónde se puede usar un procesamiento de flujo continuo?
- ¿Dónde se necesitará usar un sistema de jalar del supermercado, con el fin de controlar la producción de los procesos anteriores?
- ¿En qué punto específico de la cadena se programa la producción?
- ¿Cómo se nivelará la mezcla de producción en el proceso?
- ¿Qué incremento de trabajo se liberará y se llevará sistemáticamente al proceso?
- ¿Qué mejoras al proceso serían necesarias para que el flujo de la cadena de valor sea el diseño deseado para el estado futuro?
- Se pueden agregar todas las preguntas que permitan una mejor visualización del VSM del estado futuro para cada caso en particular, las anteriores son ejemplos y no limitativas.
La mejora en la cadena de valor es responsabilidad primaria del equipo seleccionado y del gerente y no pueden delegarla. Se pueden preguntar enfrente de las líneas de trabajo cómo eliminar el desperdicio, pero sólo la gerencia tiene la perspectiva de ver el flujo total al ser particionado en departamentos secuenciales con límites funcionales, por lo que se debe estar firmemente atento a tener lo siguiente:
- Esfuerzos constantes para eliminar la sobreproducción.
- Una firme convicción que puede ser adoptada para trabajar en su sitio.
- Contar con personal con actitud positiva, mente abierta y que busque una mejora constante.
- Buscar la aportación de todos los trabajadores con mejoras continuas pequeñas.
- Cambiar la organización y combinar productos y multihabilidades de los operadores.
- Deberá existir una total participación de todo el mundo.
- Implementar la cultura de manufactura esbelta.
- Contar con un enfoque de encontrar la causa raíz que obstaculiza el logro programado.
- Contar con una entrega total que requiere mucha transpiración e inspiración para lograr la meta.