11.1 Tipos de layout
El layout se define como
El agente asociado a la organización física, el esqueleto o a la forma adoptada por el sistema de manufactura para cumplir con sus funciones y objetivos de producción específicas.
Por tanto, la funciones del layout son las mismas que las que se pretende conseguir con el sistema de manufactura, en otras palabras se busca tener un sistema de manufactura flexible o un sistema de manufactura esbelto, se tiene que desarrollar un layout que permita conseguir estos objetivos de producción.
Entender la función del layout en los sistemas de manufactura resulta más fácil de explicar a partir de la influencia que el layout tiene en las propiedades del sistema de manufactura, a continuación se enlistan las principales propiedades o variables de influencia del layout en los sistemas de ensamble:
- Los requerimientos de espacio, el layout está asociado con la propuesta de configuración o arreglo físico de los agentes del sistema de manufactura (productos, tecnologías de proceso, tecnologías de herramental, automatización, entre otros), por ello el área requerida dependerá del tipo de configuración de layout propuesto, algunas veces el layout tiene que ajustarse a los espacios existentes en las plantas de producción.
- El grado de flexibilidad, la definición del layout define si un sistema es capaz de producir un alto volumen con poca variedad de productos o gran variedad de productos con lotes moderados de producción.
- Qué tan esbelto es el sistema, el layout tiene un impacto directo en aspectos como las distancias de recorrido o los porcentajes de utilización de los equipos de producción, al igual que en el tamaño de los inventarios (de componentes, de producto en proceso y de producto terminado).
- La robustez del sistema para reaccionar de manera ágil a variaciones en los volúmenes de producción, es decir, la facilidad para escalarse en caso de un incremento de volumen o de reducir la capacidad de producción a caídas de volumen, lo anterior sin afectar a la rentabilidad del sistema de producción.
- La modularidad del sistema que tiene impacto en la flexibilidad de configuración del sistema para diferentes mercados o localidades de producción, en este aspecto el layout permite aspirar a un diseño de producción global con variantes que se ajustan de acuerdo a la localidad de producción, como puede ser ajustar el nivel de automatización con base en los costos de mano de obra de cada localidad global.
- La robustez del sistema para reaccionar a imprevistos o emergencias como paros de línea por falla en las tecnologías de proceso, en este caso el diseño de layout con múltiples líneas de bajo volumen puede resultar en un desempeño más robusto que una sola línea de alto volumen, sin embargo hay que tener en cuenta los indicadores económicos en todo momento.
- La calidad de trabajo para las personas que operan el sistema de producción, aquí se encuentran aspectos como distancias diarias recorridas por el operario, el nivel ergonómico, el nivel de seguridad (alturas de trabajo, máximo peso a manipular, confinación de humos, rayos peligrosos o nocivos, protección contra coaliciones o impactos, entre otros), también influye en el nivel de habilidades requeridas, por ejemplo la especialización o el conocimiento de múltiples procesos o tareas.
- En los niveles de consumo energético, aunque el consumo energético está directamente asociado a los consumos de las tecnologías de manufactura para realizar una tarea en particular, la influencia del layout influye más bien en la cantidad de estaciones y equipos óptimos requeridos para cumplir los niveles de producción requeridos, desde esta perspectiva un mal diseño de layout es poco eficiente desde el punto de vista energético.
- La evolución del sistema, en este aspecto el diseño del layout permite que el sistema de producción tenga o no la capacidad de adaptarse a los cambios o evolución tanto del mercado como de los productos, este es un aspecto importante para el desempeño el del horizonte de largo plazo del ciclo de vida del sistema.
- La secuencia de ensamble del producto, una u otra secuencia de ensamble permite diferentes alternativas de layout, lo cual repercute tanto en el desempeño del producto ensamblado (dimensional o de calidad) como en el desempeño del proceso mismo (eficiencia, tiempo total de proceso, control del proceso, entre otros).
Proponer un diseño de layout exige una visión holística y al mismo tiempo creativa porque es uno de los agentes más importantes, pero al mismo tiempo más abstractos del sistema de manufactura, a continuación se muestra una propuesta para clasificar los diferentes tipos de layout, sin embargo es tan solo una referencia para el ingeniero de diseño, ya que existen muchas más alternativas que podrían ser propuestas para cualquier requerimiento de producción específico:
Haz clic para revisar el detalle
Es un layout también conocido por el nombre de layout tipo taller o funcional (figura 1), en esta configuración los equipos y tecnologías son organizados de acuerdo a procesos o funciones similares. Por ejemplo, se tiene un taller mecánico automotriz con área específica para el proceso de hojalatería, otra área específica para inspección y revisión mecánica , otra área específica para el proceso de pintura y finalmente una área específica para el lavado, en este caso el producto viaja entre diferentes áreas de proceso dependiendo de los requerimientos de cada vehículo. Otro ejemplo típico de uso de este layout es en talleres de prototipos, algunas características de este tipo de layout son:
- Bajo volumen de producción con variabilidad en la demanda.
- Alta variedad de productos.
- Variedad en secuencias o rutas de proceso.
- Inversión de capital baja y costos de operación altos.
- Operarios con habilidades múltiples.
- Equipos de uso general para varios productos.
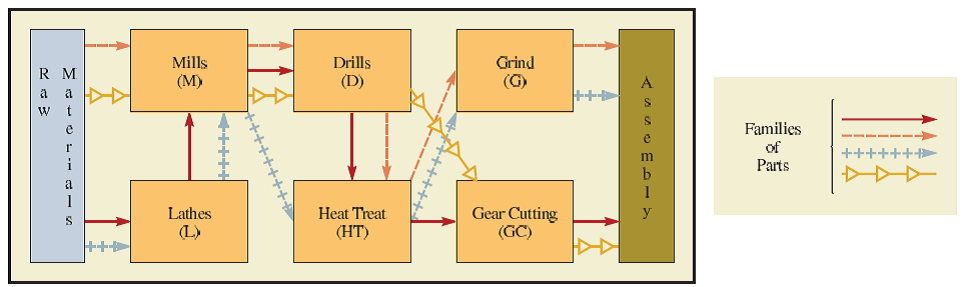
Figura 1. layout de proceso.
Fuente: Chase, J. y Aquilano, N. (2006). Administración de la producción y operaciones para la ventaja competitiva (10a ed.). México: McGraw Hill.
Es un layout también conocido por el nombre de layout de flujo de producto o ensamble (figura 2) en este caso los equipos o estaciones de trabajo son configurados a una secuencia progresiva de ensamblaje o fabricación del producto, el trayecto de cada producto es en forma de una línea, es por eso que una línea de ensamble sigue este tipo de configuración, ejemplos de este caso son la líneas de producción automotriz, o de electrodomésticos entre otros, algunas características asociadas a este tipo de layout son:
- Alto volumen de producción con mínima variabilidad en la demanda.
- Poca variedad de productos.
- Secuencias o rutas de proceso fijos.
- Inversión de capital alta y costos de operación bajos.
- Operarios con especialidad en una tarea.
- Equipos especializados para un producto.
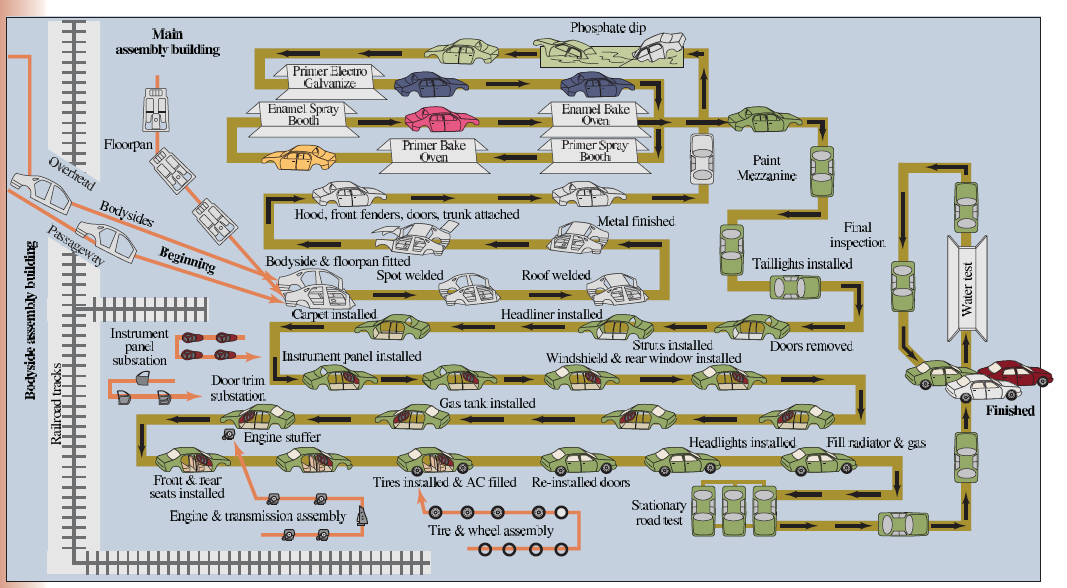
Figura 2. layout de producto, línea de ensamble final automotriz
Fuente: Chase, J. y Aquilano, N. (2006). Administración de la producción y operaciones para la ventaja competitiva (10a ed.). México: McGraw Hill.
Es un layout donde se configuran diferentes tecnologías en forma de centros de trabajo o celdas para trabajar en productos que tienen formas y requerimientos de procesos similares (figura 3), este layout es semejante al layout de proceso, en cuanto que cada celda se diseña para un proceso específico y es semejante al layout de producto en cuanto a que las celda son dedicadas a una variedad de productos limitada, sólo aquellos pertenecientes a un grupo tecnológico, las características de este tipo de layout son:
- Volumen de producción mediano con variabilidad moderada en la demanda.
- Moderada variedad de productos, limitada por los grupos tecnológicos.
- Secuencias o rutas de proceso fijos.
- Inversión de capital moderada y costos de operación moderados.
- Operarios con especialidad en una tarea.
- Equipos especializados para varios productos del mismo grupo tecnológico.
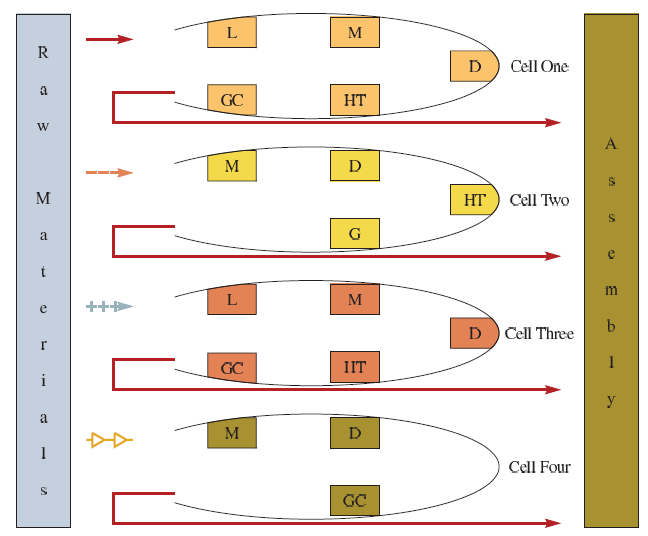
Figura 3. layout por grupo tecnológico o celular
Fuente: Chase, J. y Aquilano, N. (2006). Administración de la producción y operaciones para la ventaja competitiva (10a ed.). México: McGraw Hill.
Es un layout donde el producto se mantiene en una sola posición (figura 4), mientras que los equipos o tecnologías de manufactura son movidos para procesar el producto en su posición fija, las características de este tipo de layout son:
- Volumen de producción unitaria, productos muy pesados y difíciles de mover como barcos, algunos casos de producción de aviones o naves espaciales, entre otros.
- Poca variedad de productos.
- El producto está fijo y los procesos se programan en secuencia.
- El producto es de alto costo, mientras que las tecnologías de fabricación pueden ser de costo moderado.
- Operarios con especialidad en múltiples tareas.
- Equipos especializados para varios productos similares.
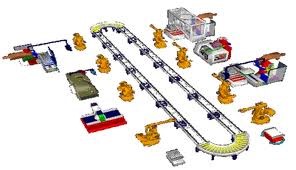
Figura 4. layout de posición fija
Fuente: https://sites.google.com/site/orgindustrialcomplementaria/disposicion-de-las-maquinas/distribucion-de-la-planta. Solo para fines educativos.
En la realidad se puede observar diferentes combinaciones de layout en una misma planta de producción. Por ejemplo, en algunas plantas de producción automotriz se pueden tener layouts de producto en las líneas de montaje final y de ensamble de carrocería para aquellos vehículos de alta demanda de producción (asociado con producción en masa); también se puede encontrar layout celular o por grupo tecnológico para producir múltiples versiones de productos con arquitecturas similares (asociados con producción flexible de segmentos de vehículos de mediano lujo), también se puede encontrar layout de producción tipo taller o proceso para aquellos segmentos de vehículos deportivos de muy alto rendimiento o de lujo.
Existen múltiples alternativas para configurar un layout, lo importante es seleccionar el diseño de que cumpla con los requerimientos del cliente en el corto y largo plazo del ciclo de vida del producto.
11.2 Criterios de selección del layout de producción
El layout es muy importante para el diseño y operación de un sistema de manufactura, un buen diseño de layout es una ventaja competitiva por facilitar el flujo de material e información, mejorar las condiciones de trabajo de las personas, mejorar el desempeño de un producto ensamblado y el desempeño de los procesos de ensamble.
A continuación se formula algunos principios o criterios que nos permiten evaluar un layout de forma cualitativa y que hay que tener en cuenta al momento de desarrollar o seleccionar un diseño de layout:
- Flujos de línea rectos o con formas adaptadas (tipo U), esta condición favorece el flujo de material y resulta en una mejor identificación de los cuellos de botella, mayor posibilidad para compartir tareas o estaciones de trabajo entre operarios.
- Evitar flujos de retorno, esta condición reduce complejidad en el manejo de materiales y permite mejorar la detección de estaciones problema.
- Tiempo de producción predecible, en este aspecto es importante combinar estaciones manuales con tareas automáticas que permitan mantener el ritmo de producción predecible y estable, que por diseño no se tenga variabilidad en el tiempo de ciclo de la línea de ensamble, para esto es importante observar el cumplimiento del tiempo de ciclo para cada una de las estaciones de la línea de ensamble.
- Evitar o reducir al mínimo la cantidad de producto en proceso entre estaciones de la línea de ensamble, esto además de reducir los costos por inventario le da agilidad al sistema al reducir el tiempo total de proceso.
- Diseñar con estaciones de trabajo de fácil visualización para las personas, esto tanto por seguridad como por permitir la fácil identificación de oportunidades de mejora o problemas.
- Implementar acciones de mejora para resolver los problemas cuellos de botella que se definen como las estaciones más lentas o con más frecuencia de paro.
- Mantener las estaciones de trabajo lo más cercano posible, tanto por reducir las distancias de manejo o traslado como por ahorro de espacio y costos asociados por servicios y construcción de naves de producción, además que facilita la flexibilidad de asignar un operario a múltiples estaciones en caso de bajas de volumen.
- Orden en el almacenamiento y manejo de material, en este aspecto es importante la trazabilidad del producto para identificar de forma fácil y rápida los lotes de producto sospechoso en caso de un problema de calidad.
- Evitar el sobre manejo innecesario de los componentes y productos, esto es puramente desperdicio y sobrecosto.
- Fácil de ajustarse a los cambios de condiciones en los mercados y productos, que el layout pueda reconfigurarse a nuevos productos o a variaciones en la demanda de producción.
- Maximizar el porcentaje de valor agregado a través de un diseño esbelto que permita la alta utilización de los activos, algunas recomendaciones son: utilizar dispositivos de indexado para realizar trabajos de proceso y de carga/descarga de material de forma simultanea para evitar que los trabajos que no agregan valor sean parte del tiempo de ciclo, aumentar la cantidad de proceso realizado por estación de trabajo a través de incrementar la velocidad de proceso o la densidad de robots, esto para reducir al mínimo la cantidad de estaciones por línea de ensamble y los requerimientos de área de producción.
- Diseñar con procesos más rápidos en las estaciones de inicio de la línea de ensamble como en los subensambles para con esto evitar cuellos de botella en línea de ensamble principal.
Puedes observar que la figura 7 compara diferentes alternativas de layout con sus ventajas y desventajas de manera cualitativa.
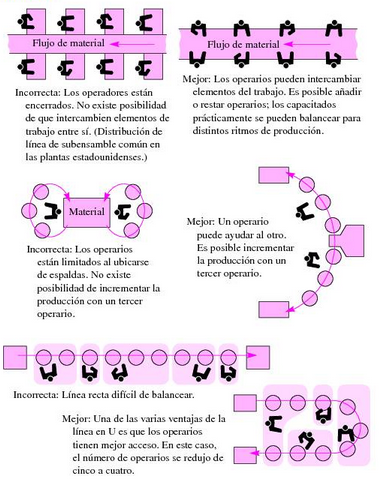
Figura 7. Criterios cualitativos para el diseño de layout
Fuente: Chase, R., Jacobs, F. y Aquilano, N. (2011). Administración de operaciones. Producción y cadena de suministros (13a ed.). EE.UU.: McGraw Hill/Irwin.
Existen otras dimensiones o criterios que nos permiten evaluar diferentes alternativas de layout de forma cualitativa y que a continuación se enlistan:
- Área requerida en m2, esto es básicamente el área ocupada por la línea de ensamble incluyendo estaciones de trabajo, almacenes y pasillos.
- Cantidad de gente requerida para operar básicamente la cantidad de operarios directos requeridos para operar la línea de ensamble.
- Cantidad de robots o equipos de automatización requeridos incluyendo tareas de proceso, de manejo y de indexado.
- Cantidad de herramentales de ensamble requeridos.
- Cantidad de estaciones de trabajo requeridas, esto tiene que ver con la cantidad de pasos requeridos para completar un producto en la línea de ensamble.
- La distancia y tiempo de recorrido del producto desde la primera estación de ensamble hasta la última estación del ensamble final.
Puedes observar que la figura 8 compara diferentes alternativas de layout con sus ventajas y desventajas de manera cuantitativa (localización de áreas de trabajo que permita distancias recorridas óptimas que aseguran costos de manejo mínimos).
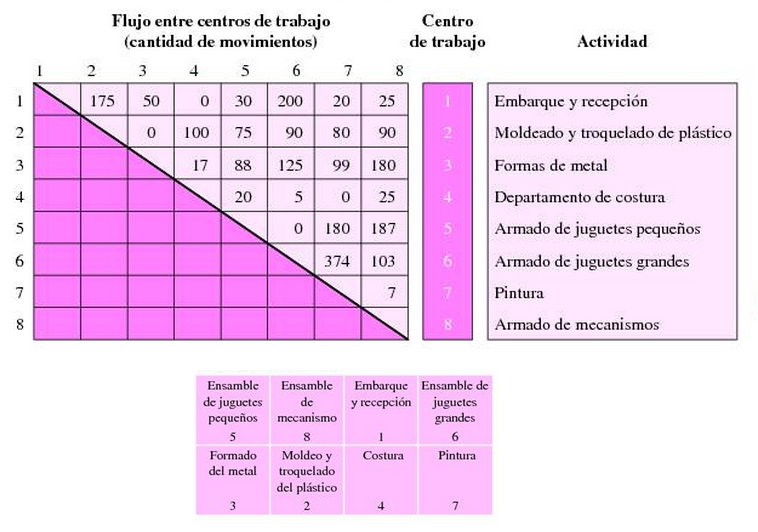
Figura 8. Tabla con cantidad de movimiento del material/producto entre los diferentes departamentos de una fábrica de juguetes de bajo volumen, incluyendo layout propuesto para reducir costos por manejo
Fuente: Chase, R., Jacobs, F. y Aquilano, N. (2011). Administración de operaciones. Producción y cadena de suministros (13a ed.). EE.UU.: McGraw Hill/Irwin.