8.1 Herramentales de sujeción e indexado
En una línea de ensamble los herramentales de sujeción tienen las siguientes funciones:
- Garantizar las tolerancias dimensionales de los ensambles. En este sentido los herramentales son diseñados para localizar y sujetar el producto o ensamble en las zonas críticas.
- Controlar los efectos o influencias de variabilidad dimensional asociadas con los procesos en particular, por ejemplo, los procesos de soldadura son una fuente de calor de entrada al producto, lo cual causa su deformación térmica; o en un proceso de maquinado las fuerzas de la herramienta de corte provocan un sobre la pieza de trabajo. En ambos casos los dispositivos de sujeción consideran elementos de clamp o sujeción dentro de su diseño, que ayudan a contrarrestar las fuerzas ejercidas en el producto durante el proceso.
Los principales componentes o elementos de un herramental de sujeción o ensamble son los siguientes:
- Elementos mecánicos de apoyo y pilotaje. Son componentes diseñados de acuerdo a la geometría, localización y tolerancia dimensional marcada por el diseño del producto en los planos de dimensionamiento geométrico y de tolerancias del producto (GD&T). Estos componentes tienen que ser fabricados con materiales de alta durabilidad y con alta precisión mecánica, ya que son las referencias físicas que garantizan la calidad dimensional del ensamble.
- Elementos de clamp o sujeción. Estos componentes proveen la fuerza mecánica requerida para asegurar la estabilidad dimensional del producto durante la aplicación de los procesos de ensamble o manufactura (unión, soldadura, maquinado, etc.). Los clamps son actuadores neumáticos, hidráulicos, eléctricos o magnéticos, dependiendo de los requerimientos del producto y el tipo de proceso que se desee utilizar.
- Dispositivo de control con válvulas y módulos de comunicación. Para asegurar la integración y coordinación de los dispositivos con los demás elementos de la celda o línea de producción, dichos módulos permiten la comunicación de los sensores y válvulas de control de los clamps con el control central de la celda. Para tal efecto estas interfaces se comunican a través de un bus de campo como profibus, interbus o devicenet. Se puede decir que estos módulos de comunicación están ubicados en el segundo nivel de la pirámide de control de los sistemas automáticos.
- Sensores para garantizar la repetibilidad y correcta secuencia de ensamble de un producto. Aquí se pueden listar sensores para detectar la presencia de los componentes a ensamblar o sensores que permiten identificar el tipo de modelo o producto que se va a procesar.
- Líneas de conducción de los fluidos como aire, aceite hidráulico o cables eléctricos dependiendo del tipo de clamp o actuadores utilizados.
La taxonomía de los herramentales de ensamble pude ser definida como herramentales manuales o automáticos.
- Los manuales son aquellos cuyos elementos de clamp o sujeción son operados de forma manual por un operador.
- Los automáticos son operados por actuadores neumáticos, hidráulicos o eléctricos y procesos de control.
De acuerdo al tipo de actuadores de sujeción que utiliza, se pueden encontrar los siguientes herramentales:
- Herramentales neumáticos
- Herramentales hidráulicos
- Herramentales magnéticos
- Herramentales eléctricos
De acuerdo al grado de adaptabilidad del dispositivo asociado con la capacidad de sujetar múltiples modelos o familias de productos, existen las siguientes clasificaciones:
- Herramentales dedicados (aquellos que sólo son diseñados para procesar un producto).
- Herramentales flexibles son diseños de herramental intercambiables que permiten el procesamiento de varios productos con tiempos de cambio cortos.
- Herramentales reconfigurables (aquellos diseños de herramental que permiten ser reconfigurados para otro producto)
- Herramentales programables o adaptables. Son más cercanos a un robot industrial, en este caso de configuración cartesiana. Permiten el cambio rápido de la configuración del herramental para diferentes productos.
El herramental es un agente muy importante del sistema o línea de ensamble, principalmente porque no sólo influye en la calidad dimensional del producto, si no que también facilita o restringe la flexibilidad de procesar diferentes productos en una misma línea de ensamble.
Los principales atributos a considerar en el diseño y selección de un herramental de sujeción o ensamble son los siguientes:
- Nivel de fuerza de clamp requerida.
- Zonas críticas de registro y clamp.
- Grado de repetitividad y reproducibilidad.
- En algunos casos el peso del herramental.
- El tiempo de ciclo asociado con la tarea de carga y descarga del producto.
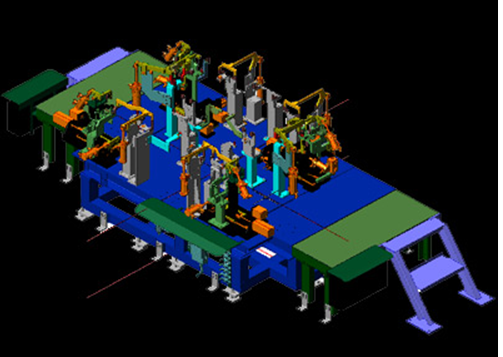
Figura 1. Dispositivo de sujeción para el ensamble de un piso frontal de automóvil
Imagen obtenida de http://www.kk-hid.co.jp/...
Sólo para fines educativos
8.2 Dispositivos de transferencia y manejo
La función de los dispositivos de transferencia es el manejo del producto en proceso o terminado dentro de la línea de ensamble. A continuación se listan las principales tareas de estos agentes:
- Carga y posicionamiento del producto en proceso o componentes en los dispositivos de sujeción o estación de trabajo.
- Descarga del producto en proceso de los dispositivos de sujeción o estación de trabajo.
- Transferencia del producto en proceso a la siguiente estación de trabajo o estaciones de almacenamiento en línea o al final de la línea como producto terminado.
Los principales componentes o elemento de un sistema de transferencia o manejo son los siguientes:
- Elementos mecánicos y de clamp para la sujeción del producto en proceso. A estos elementos también se les puede dar el nombre de garra o gripper. Los actuadores empleados para sujetar la pieza de trabajo pueden ser neumáticos, eléctricos, magnéticos o de vacío, dependiendo del peso, geometría y dimensiones de la pieza de trabajo.
- Elementos mecánicos y transmisión motriz del sistema de transferencia. Estos elementos son aquellos componentes que permiten la transferencia de la pieza de trabajo a la próxima estación, dependiendo del diseño o tipo de unidad de transferencia. Por ejemplo, en un transfer tipo monorriel electrificado el sistema motriz es un carro moto-reductor lineal, mientras que el elemento que permite la transferencia de la pieza es un riel electrificado por donde corre el carro de transferencia con el producto a transferir.
- Dispositivo de control con válvulas y módulos de comunicación, sensores para garantizar la repetitividad en la transferencia de una pieza de trabajo y líneas de conducción de los fluidos como aire, aceite hidráulico o cables eléctricos.
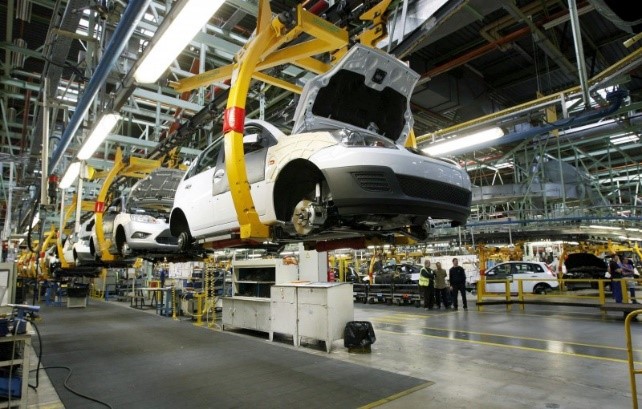
Imagen obtenida de www.efemotor.com
Solo para fines educativos
La taxonomía de los sistemas de transferencia pude ser definida como sistemas de transferencia manuales o automáticos.
- Manuales: son aquellos cuyos elementos de clamp o sujeción son operados de forma manual por un operador (por ejemplo un polipasto).
- Automáticos: son operados por robots o sistemas automáticos.
Existen diferentes transferidores de acuerdo al tipo de montaje del sistema de transferencia:
- Transferidores sobre cabeza montados por encima de la estación de trabajo, que mueven el producto por arriba de la estación de trabajo
- Transferidores a nivel de piso que mueven el producto por arriba de la estación de trabajo.
De acuerdo al grado de flexibilidad del dispositivo asociado con la capacidad de sujetar múltiples modelos o familias de productos o la flexibilidad para modificar la trayectoria o ruta del camino de la transferencia, se encuentran los siguientes sistemas:
- Sistemas de transferencia con trayectoria fija, como un walking beam conveyor.
- Sistemas de trayectoria reprogramable, como un robot de manejo con garra de manejo intercambiable.
- Un vehículo autómata guiado (AGV).
- Otros sistemas reconfigurables como conveyors tipo pallet lineales, con capacidad de reconfigurar su layout físico.
El sistema de transferencia es un agente muy importante del sistema o línea de ensamble, principalmente porque influencia el valor agregado durante el tiempo de ciclo, es decir, entre más lenta sea la transferencia menor será el tiempo de proceso disponible. También porque facilita o restringe la flexibilidad de procesar diferentes productos o modificar el layout o secuencia de ensamble en una línea de ensamble.
Principales atributos a considerar en el diseño y selección de un sistema de transferencia:
- Nivel de fuerza de clamp requerida.
- Zonas críticas de sujeción.
- Grado de repetitividad y reproducibilidad.
- Capacidad de carga (peso de la pieza de trabajo).
- El tiempo de ciclo asociado con la tarea de carga y descarga y transferencia del producto.
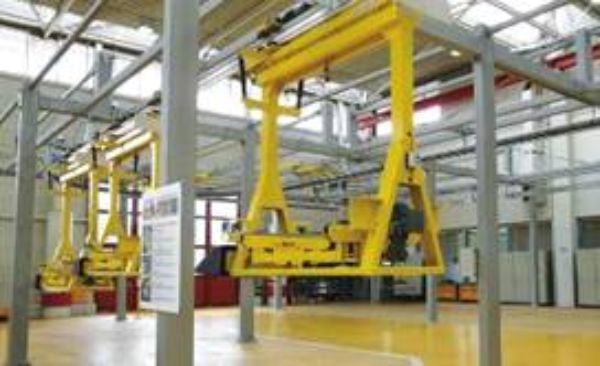
Figura 2. Sistema de transferencia tipo monorriel electrificado
Imagen obtenida de http://www.eisenmann.com/...
Sólo para fines educativos
8.3 Dispositivos de control y supervisión de producción
Las principales funciones de los sistemas de control y supervisión son las siguientes:
- Coordinar las secuencias de control discreto entre los diferentes agentes y elementos de la celda o línea de ensamble; por ejemplo coordinar la carga de la pieza de trabajo, la ejecución del proceso y la salida y transferencia de la pieza de trabajo a la próxima estación.
- Comunicar instrucciones a los trabajadores (recibir tratamiento o instrucciones de ensamble de la unidad de trabajo específica).
- Programas de descarga de piezas a las máquinas controladas por computadora.
- Planificar y contabilizar la producción.
- Diagnóstico de fallos cuando se produzcan errores en línea.
- Control de la seguridad (proteger al operario y técnico de mantenimiento).
- Control de calidad (detectar y rechazar las unidades de trabajo defectuosas producidas por el sistema).
- Gestión de operaciones (gestión de operaciones globales, diagnóstico y solución a problemas de programación de forma remota).
Los principales componentes de un sistema de control y supervisión son éstos:
- Controlador lógico programable (PLC): como unidad de control permite la programación y coordinación de las secuencias de control discreta procesando las órdenes y condicionantes para la ejecución de las diferentes tareas de colaboración que tienen que ejecutarse en la celda o línea de ensamble.
- Los módulos y redes de comunicación industrial: permiten la transferencia de información crítica del proceso entre los diferentes agentes de la línea de ensamble y el PLC. También existen redes de comunicación a un nivel superior que facilitan la comunicación y transferencia de datos a otras áreas de soporte de la producción, como diseño del producto, calidad o planeación de producción, consiguiendo arquitecturas de manufactura integrada por computadora tipo CIM o habilitando los conceptos de administración de la vida del producto (PLM).
- Las interfaces hombre-máquina (HMI): permiten la interacción entre el operario y la celda automática. Éstas pueden ser microprocesadores con pantallas y aplicaciones gráficas integradas o computadoras con aplicaciones gráficas de supervisión de proceso central avanzado tipo SCADA (supervisión, control y adquisición de datos).
- Los dispositivos de seguridad tipo botones de paro de emergencia, cortinas de luz, fotoceldas o escáner, requeridos para la protección del operario y de los técnicos de mantenimiento de la celda.
La diferentes arquitecturas de los sistemas control y supervisión que existen en una línea de ensamble discreta son las siguientes:
- Arquitectura de control descentralizado: un sistema de control es asignado a cada una de las estaciones o celdas de trabajo, lo que permite una mayor independencia y facilita el diagnóstico de los fallos en la línea de ensamble.
- Arquitectura de control centralizado: en este caso un solo sistema de control es capaz de coordinar y supervisar la línea de ensamble completa o varias celdas o estaciones de trabajo. Esta arquitectura de control permite reducir los costos, pero con un menor grado de modularidad e independencia entre las diferentes estaciones o celdas de una línea de ensamble.
- Arquitectura de control integrada por computadora (CIM): esta arquitectura de control integra no solamente las estaciones de producción, si no también otras tareas asociadas con las áreas de soporte a la producción, como diseño del producto (CAD), análisis del producto (CAE), simulación y validación del proceso, control de calidad del producto, planificación y análisis de la producción.
El sistema de control es un agente muy importante del sistema o línea de ensamble, principalmente porque influencia la robustez del sistema de producción y la facilidad de diagnóstico o mantenimiento de una celda o línea de ensamble. Además es un agente que facilita la integración entre el sistema de producción y las demás áreas de soporte. También facilita o restringe la flexibilidad de modificar el layout en una línea de ensamble (control modular descentralizado vs. control centralizado).
Principales atributos a considerar en el diseño y selección de un sistema control y supervisión:
- Capacidad de memoria para almacenamiento de datos, programas e imágenes.
- Velocidad de procesamiento o escaneo.
- Velocidad de transferencia de datos.
- Capacidad de módulos y número de entradas o salidas.
- Conectividad y adaptabilidad a diferentes dispositivos de control y protocoles de comunicación.
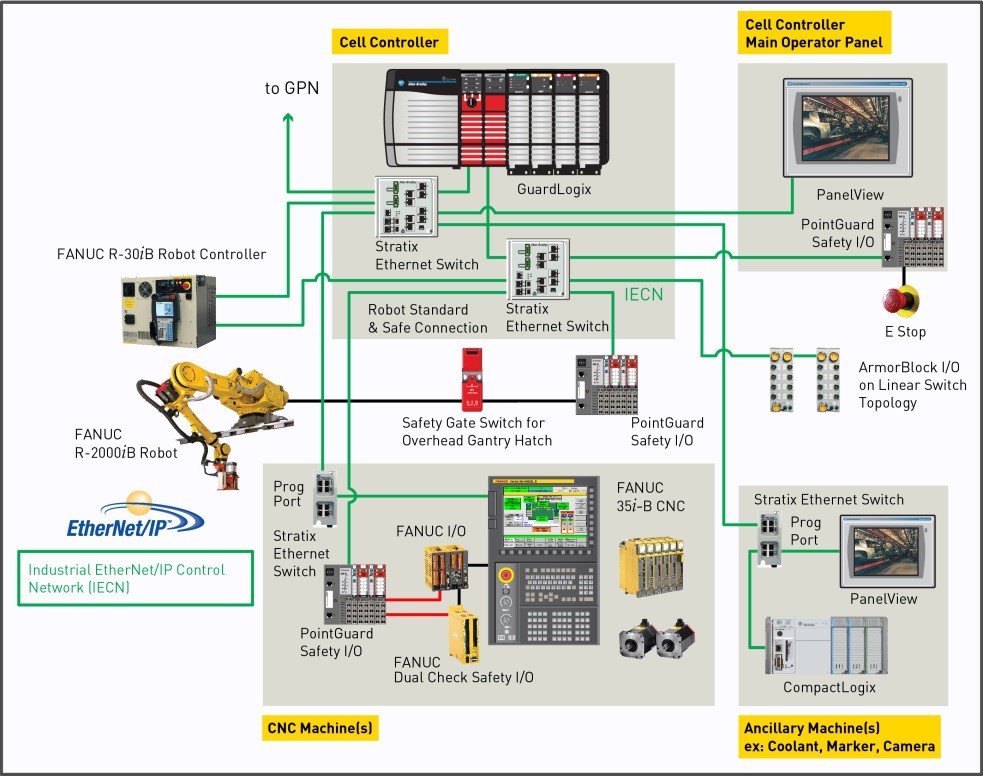
Figura 3. Sistema de control integrado para robot-CNC y equipos periféricos
Imagen obtenida de http://www.fanucamerica.com/...
Sólo para fines educativos